In this article, Saksham Chhabra student of UPES (Dehradun) discusses how to set up a soap manufacturing plant.
INTRODUCTION
The Cosmetic industry is one of the fastest growing industries in the world with so many products and billions of consumers. Under which also comes the soap industry which is regarded as a fast moving consumer good (FMCG) and is one of the essential products in the daily uses of an individual. Soap is a product that is consumed by billions of people across the globe in different forms such as:
- Personal usage,
- Sanitary usage,
- Laundry usage,
The soap industry comes under the cosmetics industry for which specific laws have been made in the form of drugs and cosmetic act, 1940. As soap is manufactured in different form, variants, colours and sizes under different brand names and logos as per the requirements and the needs of the people who will ultimately consume it, so that they are satisfied. If a firm want to start its manufacturing operations of a product, it has to adhere to certain guidelines and rules before setting up its unit. Many reports have showed that in the coming few years 2021, the contribution of the soap manufacturing industry to the world’s economy is expected to increase at an annual rate of 0.2% and even the the Gross Domestic Product is expected to increase at 2.3% annually.
WHAT DO YOU UNDERSTAND BY THE TERM COSMETICS?
The Literal meaning of the term “cosmetics” has been specifically defined under section 3(aaa) of the Drug and Cosmetics Act 1940 and Rules 1945 which states “Cosmetics are products that are intended to be rubbed, poured, sprinkled or sprayed on, or introduced into, or otherwise applied to, the human body or any part thereof for cleansing, beautifying, promoting attractiveness, or altering the appearance” and includes any article intended for use as a component of cosmetic. For manufacturing, distribution and selling of cosmetic products license are mandatory. Thus, on the basis of which cosmetics have categorized as follows:
A)Face powder, cake makeup, compacts, face packs, masks, and rouges, Creams, lotions, emulsions, pastes, cleansing milk, shampoos, pomade, brilliantine, shaving creams and hair oils etc.
B)Nail Polishes and Nail Lacquers.
C)Lipsticks and Lip-gloss, etc.
D)Depilatories
E)Preparations used for Eyes
F)Aerosol
G)Alcoholic Fragrance Solutions.
H)Hair Dyes
I)Tooth powders and toothpaste, etc.:
J)Toilet Soaps
WHAT IS THE PROCEDURE FOR OBTAINING PERMISSION TO START MANUFACTURING OF A SOAP UNIT?
It is advisable for a soap manufacturing business to be set up as a Limited Liability Partnership (LLP) or Private Limited Company as the investment in plant and machinery and the turnover of the firm would be in excess of more than 25 lakhs. Further, an LLP or a Private limited company form of business would ensure that the unit can easily be granted loans by the banks and is transferable in the future. As per the Drugs and Cosmetic rules act of 1940, it provides that the rules and regulations in this regard are framed by both the central and the state government regarding the issuing of licenses to individuals for their business. Ultimately, it is the state drug authorities of the various states that have got the power to issue licenses. A person who wishes to get the license for manufacturing soap can get it in 7 Simple Steps under the drugs and cosmetic rules:
STEP 1-Firstly, a person applying for a manufacturing license for handmade soap needs to fill the Application Form 31 and the person is required to pay an amount of Rs 3,500 and Rs 2,500 as a government and inspection fee of 2500 respectively with the form and an inspection fee of Rs 1000 at every inspection.
STEP 2- Secondly, the cosmetics products for which the license is being acquired should be specified into classes of cosmetics, as has been mentioned under Schedule M-II, where the cosmetics have been classified into 10 categories so that proper analyzing can be done.
STEP 3- A person applying for the license of manufacturing handmade soap or any other cosmetics should have passed the intermediate exam with Chemistry as one of its subject or any examination which is recognized by the Licensing authority.
STEP 4-Apart from it to get a license it is required to hold a diploma in Pharmacy which should be certified and approved either under the Pharmacy Council of India under the Pharmacy Act, 1948 or under the Pharmacy Act, 1948.
STEP 5-At the time of applying for the license it is required to mention other information like the lists of equipment, manufacturing facility details with minimum area required for manufacturing, Technical Competent personnel details, etc. so that the licensing authorities have proper knowledge regarding the background of the person who will be manufacturing the product.
STEP6-Apart from those details the licensing authority also considers before approving the license that whether the cosmetic is misbranded or is a spurious cosmetic and an inspector goes to check on the premises to see that everything is followed in an appropriate manner and then make the report is made.
STEP 7– After that when the authority is satisfied with the report and the standards of your premises it grants the license and also for renewal the manufacturer is required to categories the cosmetics as per Schedule M-II.
It must be specifically noted that the licensed issued to the firm is valid for a term of a 5 years after which it is subjected to renewal. There are also certain other Documents that are to be attached with the Application at the time of getting the license issued which are as follows:
- Affidavit of Applicant attested by the court,
- List of machines installed for manufacturing the product for the complete knowledge of the licensing authorities,
- List of laboratory equipment which will be utilized in the unit in the production process,
- A Valid No Objection Certificate from Pollution Control Board in the name of the unit,
- If the Manufacturing unit is on Rent/Lease, then the copy of the rentlease agreement is to be attached,
- Lastly, the proper plan layout and structure of the premises of the producing unit.
WHAT ARE THE LAWS AND STANDARDS THAT A SOAP PRODUCING UNIT IS REQUIRED TO ADHERE TO?
There are certain laws that the government has made for the Manufacturing Industry to during its operations:
LABOUR LAWS
A) THE INDUSTRIAL DISPUTES ACT, 1947: The objective of the Industrial Disputes Act is to secure industrial peace and harmony by providing machinery and procedure for the investigation and settlement of industrial disputes by the process adjudication, arbitration and conciliation machinery which is provided under the statute. The main objective of this act is “Maintenance of Peaceful work culture in the Industry in India” which is clearly provided under the Statement of Objects & Reasons of the statute.
B) THE TRADE UNIONS ACT, 1926: Trade Union means any combination in the form of temporary or permanent, formed primarily for the purpose of regulating the relations between workmen and employers for imposing restrictive conditions on the process and conduct of and business or trade and includes any association of two or more trade unions.
C) THE EMPLOYEES’ COMPENSATION ACT, 1923: This act is there for the payment by certain classes of employers to their [mainly employees] of compensation for injury by accident. Whereas it is feasible to provide for the payment by certain classes of employers to their workmen of compensation for injury by accident.
D) THE EMPLOYEES’ PROVIDENT FUND AND MISCELLANEOUS PROVISIONS ACT, 1952: The EPF & MP Act, 1952 is created for the purpose of social welfare and to safeguard the interests of an employee. Any factory or establishment which directly or through intermediaries like contractors have more than 20 employees are to be safeguarded under this act.
E) THE MINIMUM WAGES ACT, 1948: The Minimum Wages Act 1948 is an act made by the parliament concerning the Indian labor law that sets the minimum wages that must be paid to skilled and unskilled laborers. As per the Minimum Wages Act of 1948, State and Central Governments have the power to fix and revise minimum wages. The Act specifies that the “appropriate” government should fix the wages i.e. if the wages to be fixed are in context to any authority of the Central government or Railway administration then the Central government fixes it.
F) THE FACTORIES ACT, 1948: This act helps in assessing and formulating National Policies in India with respect to occupational safety and health in factories and docks in India. It deals with all the problems that are related to the safety,well-being, health, efficiency of the employees at the workplaces.
G) THE PAYMENT OF BONUS ACT, 1965: This act provides for the payment of bonus to persons employed in certain establishments, employing 20 or more persons, on the basis of profits or on the basis of production or productivity and matters connected therewith.
H) THE APPRENTICES ACT, 1961: The purpose of this act is to meet the increasing demand for skilled craftsmen. The facilities to be utilized that are available for training apprentices and also to ensure their training in accordance with plan programme. Also to promote new manpower skill and simultaneously training the old one to.
I) THE MATERNITY BENEFIT ACT, 1961: This act is basically established to govern and regulate the women employment and their interests across the country.The act provides 12 weeks as the maximum period for which any working woman shall be entitled to maternity benefit. She can avail this benefit as 6 weeks up to and including the day of her delivery and 6 weeks immediately following the day of her delivery.
J) THE PAYMENT OF GRATUITY ACT, 1972: In India gratuity is a type of retirement benefit. It is a payment made with the intention of helping an employee financially after his retirement. It was held by the Supreme Court of India in the case of Indian Hume Pipe Co Ltd v Its Workmen, that the general principle underlying gratuity scheme is that by service over a long period the employee is entitled to claim a certain amount as the retirement benefit. The Payment of Gratuity Act was passed by Indian Parliament on 21 August 1972.
K) THE CHILD LABOUR (PROHIBITION AND REGULATION) ACT, 1986: This act is one of the most important act and is also one the most debated acts regarding children in India. It outlines where and how children can work and where they can not. The provisions of the act are meant to be acted upon immediately after the publication of the act, except for part III that discusses the conditions in which a child may work and also Part III can only come into effect as per a date appointed by the Central Government. This act was formed so that so child below the age of 14 years is not put into employment for the protection of his interests.
LEGAL METROLOGY ACT, 2009
The legal metrology act which came in the year 2009 with the objective to establish basic essentials for the weight and measures of the goods which are sold in the terms of their weight in the regulation of the trade and commerce in the country. The section 2(g) of this act basically states in relation to the treatment of units with proper measurement in relation to the mandatory technical and legal requirements from the point of view of the public to ensure their safety and protection from the goods they intend to buy.
The manufacturers are required to keep a record of all the things they produce and their proper documents of the list of standards. Also if they manufacturing unit advertises their product then they should specify the necessary details on the product such as the content, quantity, weight and the retail price. Also, section 23 of the act clearly states that the license to make, sell and distribute such goods are to be issued by the controller for certain specific time period or any other things on the payment of the fees as prescribed at the time of registering for the license. Afterwards, proper verification and stamping by the government authorities is done.
The Act was basically passed to govern and see that no manufacturer or repairer of the goods does anything that could hurt the interests of the public at large and if any such act is done then the act provides for various penalties for various offences and illegal acts. Thus, the act works for the smooth working of the trade and commerce in the country and is a boon to the society.
ENVIRONMENTAL COMPLIANCES
The National Green Tribunal Act, had been setted up in the year 2010 for the protection of the environment and to see that their is proper follow up and implementation of the policies and procedures. Section 4 of the environment pollution and rules act states that, every individual carrying out an industry, process or operation that requires consent from the State Pollution Control Board (SPCB) as per Water (Prevention and Control of Pollution) Act, 1974 or the Air (Prevention and Control of pollution) Act, 1981 or authorization under Hazardous Wastes (Management and Handling) Rules, 1989 must submit an “Environmental Statement” for the financial year ending 31st March in the Form V to the concerned SPCB on or before the thirtieth (30th) day of September every year. EIA involves prediction of environmental consequences of any developmental project and is an indispensable asset. Diverse types of pollutions have emerged with the progress of man and his innovations. Industrial revolution all over the world has lead to the advancement of our technologies and lifestyle, however, the most severe adverse effect of this revolution is pollution. Almost all types of pollutants found on this planet are traceable to some industry or the other including the agriculture industry. Diverse forms of industrial wastes be it gases, liquids or solids are ultimately released into the environment either in the air, water bodies or into landfills. Air pollution is ranked as the most severe type of pollution of all, resulting in approximately 4.6 million deaths annually as per the world health organization.
There are certain environmental laws that the manufacturing unit is required to follow and adhere to while performing its operations such as:
- Water Prevention and Control of Pollution,1974
- Air Prevention and Control of Pollution Act,1981
- Environment Protection Act,1981
- Wild Life protection Act,1972
- Biological Diversity Act,2002
- Forest Act,1980
- Public Liability Insurance Act, 1991
Thus, to protect and safeguard the interests of the people and the society at large the manufacturing units have to adhere to the following laws.
WHAT ARE THE RULES AND REGULATIONS THAT ARE APPLIED TO SOAP MANUFACTURING UNIT?
The rules and regulations that are in need to be followed by the soap manufacturing unit are as follows:
- According to the Biomedical waste rule, proper arrangements have to be made for the disposal of the waste so that any kind of pollution is caused and any kind of problem or disease is not caused to anybody.
- The Factory should have proper sanitation facilities, hygiene should be maintained in the manufacturing building, proper gloves and emergency facilities for the labors.
- The production house or factory should not be established near residential areas as there is a risk of pollution and contamination which may cause distress and problems to the people living in the area nearby which might result in the death of the people.
- If your premises or factory etc is not following the provision of Drugs and Cosmetics Rule then it can penalized with a fine of 5000/-.
- The basic essential things where the soap manufacturing is to look after is the expenditure which is done upon raw material, salaries and wages, power cost and receivables. The Raw Material should be of Rs.2.5 lakhs on-stock to carry on its operations smoothly and also an additional capital of Rs.1 to 2 lakhs for other expenditures like salaries, power and receivable. Also having a good and adequate working capital only helps a firm unit to perform its goals in a good and better manner.
- The Labourers and the workers working should be given proper training and orientation so that the chances of any mishappening or any problem are reduced and also proper and adequate quality of products are produced which should be in accordance with the standards set for that particular product. Below are the certain requirements while starting the operations of a soap manufacturing firm:
- Although there appear to be no industry-specific regulatory issues affecting soap markers that they should be aware of the broader labor, occupational and environmental regulations. Big firms/unit generally have employees or the department is devoted to the following of the new regulatory developments and devising compliance procedures.
- There should be proper labelling on the product with the brand name address of the manufacturing firm and place with the price, contents, expiry and also the directions for the use of the product as per the rules laid down by the drugs and cosmetic rules of 1945 under rule 148 and the product should be in accordance of the international cosmetic standards as if they are not as per the act then it is punishable offence and the repercussions are as follow: fine upto 1000 or 1 year of imprisonment or both and if repeated consequently fine may increase to 2000 or imprisonment upto 2 years or both.
- If the person who is manufacturing the products is engaged in the process of importing and exporting goods then he has to fill the form 10 but only the government has the authority to grant permission in such matters if they are in the interest of the society.
CONCLUSION
Due to the growing population, the needs and the demands of the consumers are rising thus due to the establishment of such manufacturing units in the country it will benefit the people in fulfilling their needs and also it will also create thousands of employment opportunities for the people who are residing in the rural areas who don’t have a proper source of living for their family will benefit the most. The government has established specific norms under the Drug and Cosmetic Act 1940 and Rules 1945 which also makes the government (Centre and State) to be more powerful in making such decisions in taking important decisions for the benefits of the people. The procedures and the guidelines laid down for the registration and other legal work are quite safe and reliable which helps in the reduction of chances of the entrance of fake and other manufacturing units who produce imitated products which are of really poor quality and which may even harm the people thus the licensing process proves to very effective in this regard.
Also the government has also established many status which keep a check on these firms after they are licensed so that to keep a check upon these firms that they are performing their operations in the desired manner and there is no violation of the policies and also if there’s any problem there are redressal bodies made for the settlement of any kind of disputes and problems in the manufacturing units.
REFERENCES:
- The Drugs and Cosmetic act 1940 and rules 1945(bare provision),
- https://cliniexperts.com/india-regulatory-services/cosmetic/
- http://www.cdsco.nic.in/writereaddata/Guidelines%20on%20Registration%20of%20Import%20of%20Cosmetics.pdf
- https://mohfw.gov.in/fooddrugs/guidelines-registration-import-cosmetics
- http://envfor.nic.in/legis/env/env1.html
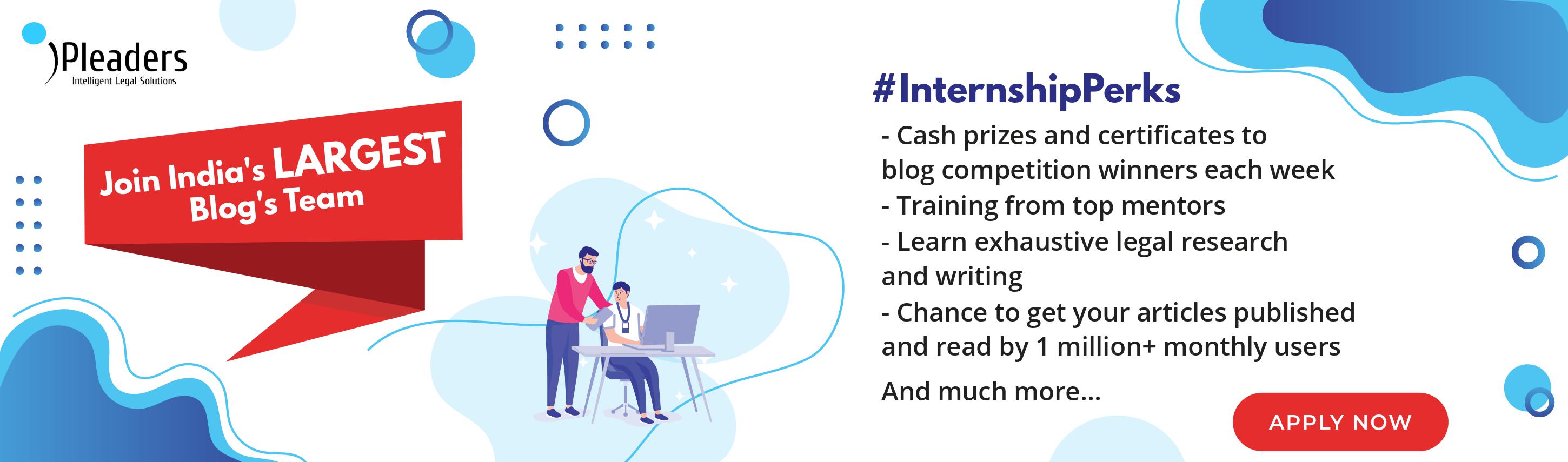