This article was written by Prabhakar Acharya, pursuing the Training program on Using AI for Business Growth Course from Skill Arbitrage, and edited by Koushik Chittella
Table of Contents
Introduction
Supply Chain Management (SCM) gained prominence as a key business concept in the late 1990s through different articles and books written by experts, professionals, and academicians. SCM is defined as the process of the broad range of activities required to plan, organise, implement, control, and manage the operations of a supply chain by executing the flow of goods and services within a supply chain involving raw material movement, its storage, handling work-in-progress inventory, and finally delivering finished products to customers. The goal is to carry out these activities in a streamlined, environmentally friendly, and cost-effective way, with the ultimate aim of satisfying customer requirements efficiently and effectively to the extent possible.
Supply Chain Management is the initial flow of information culminating in the flow of goods & services in an environmentally friendly and cost-effective manner, leading to ultimate customer satisfaction. SCM is the management of supply chain activities to gain customer value and achieve sustainable competitive advantage to optimise effectiveness and efficiency. This comprehensive process covers all aspects & coordinates from product development and sourcing to production and logistics, besides information systems. Organisations within a supply chain are interlinked through both physical and information flows, working jointly to achieve these goals. In sophisticated supply chain systems, the residual value of used products and packaging may re-enter the supply chain where their remaining value is recyclable. Supply Chain Management draws heavily on principles from procurement, operations management, logistics, and information technology, striving for a cohesive, integrated approach.
The 21st century has witnessed significant changes in the business environment that have influenced the evolution of supply chain networks. The foremost being the rise of globalisation, along with the growth of multinational companies, mergers, acquisitions, strategic alliances, joint ventures, and business partnerships, has significant key success factors enhancing previous practices like lean manufacturing, agile manufacturing, and just-in-time. Further, technological development, particularly the significant reduction in communication costs (a part of transaction costs), has led to amplified changes in active coordination among members of supply chain networks.
Methods to reduce expenses in the supply chain
Following are the three strategies to reduce supply chain expenses through sustained relationships without critically impacting your suppliers:
- Avoid redundancies: Start by mapping out all activities across your supply chain partners associated with procurement, inspection, storage, production, and transportation logistics of materials and components that constitute the WIP & finished product. On close observation, one would find that some tasks are duplicated & repeated by different supply chain partners; for example, one partner conducting an outgoing inspection followed by an incoming inspection by another. By cooperating with your partners to eliminate these redundancies, one can reduce the time and costs, which in turn culminates in lowering the overall price.
- Assigning tasks to an optimal supply chain partner: Very often, the supply chain partner’s capabilities overlap. For example, in the case of a customer purchasing embossed metal articles OR sheets, both the immediate supplier and their supplier may offer embossing services. The task should be assigned to the partner who can do it most effectively, subject to meeting the necessary required quality, delivery schedules, and service standards. This requires rethinking about traditional processes to adopt the most efficient approach so that one can do it in the best benchmarked way.
- Leverage the supply chain’s buying power: Frequently, the products and services procured by second-tier suppliers are also purchased by first-tier suppliers, who presumably get better pricing. In such cases, the first-tier supplier can very well negotiate to include the second-tier suppliers’ volume in their requirement to secure even better discounts. This approach helps in trimming total costs across the entire supply chain network.
Optimisation of supply chain
Very often, when establishing sourcing, one may encounter complexities and constraints that make supplier selection challenging. Constraints are hindrances that restrict your choices, an example being:
- One may be required to select two suppliers instead of just one to mitigate the risk of a shortfall in supplies.
- Suppliers don’t possess the capacity to handle & provide 100% of one’s business requirements.
- One might need to allocate a certain percentage of requirement orders to diversified suppliers. Further complexities, which can add challenges, can be to manage a large number of line items bid offered.
- Vendors are offering attractive discounts for different volume levels OR for select combinations of line items.
- Varied delivery locations with varying suitability of certain vendors to supply.
- Selecting between freight lanes with different costs.
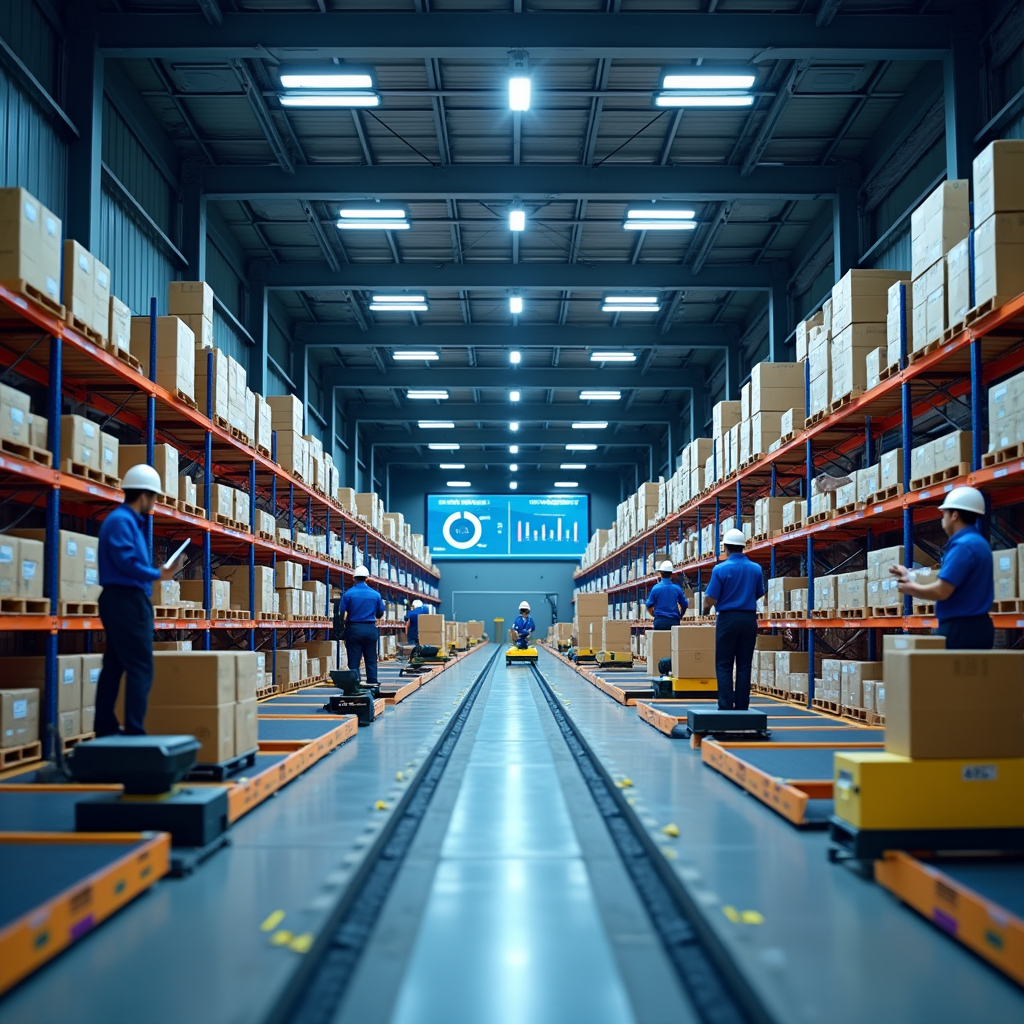
It becomes challenging to ascertain the best vendor selection when faced with multiple constraints and complexities. Under such situations to address this, purchasing departments use supply chain optimisation technology to justify their decision. The supply chain optimisation technology applies advanced mathematical techniques to analyse & evaluate a sourcing scenario to decide & establish the optimal distribution of awards. It helps purchasing departments make the best decision to benchmark among multiple possible alternatives.
Promoting competition, organisations invite multiple capable bidders/vendors to overcome constraints and complexities, leveraging a number of overwhelming potential alternatives & combinations, thus increasing the likelihood of making a suboptimal decision. Although it’s possible to manually analyse bids, supply chain optimisation technology can save time and money and reduce errors, thus making it a valuable tool for handling complex sourcing strategies.
However, for every organisation or spending category, supply chain optimisation technology may not be suitable. It is effective when used to source high-value core commodities, parts, and materials that have capacity constraints, related risks, and competitive vendors.
Since supply chain optimisation technology requires a major investment, it is typically implemented by larger organisations, which can achieve a significant return on investment due to their high spend volume. Smaller organisations or those dealing with simplistic & uncomplicated spending categories may find that the costs of implementing supply chain optimisation technology surpass the benefits.
Lean supply chain management
The lean principle in supply chain management (SCM) is associated with the elimination of waste in all forms. Waste is defined as an activity that does not add value from the customer’s perspective to the delivered product or service. The waste as identified prevails in unnecessary inventory, overproduction, excess processing, waiting times, inefficient transportation, excessive motion or handling, and defects.
The lean principle can be applied to all three flows within an organisation: i.e., information flow, materials (products, services) flow, and cash flow. For survival & generating revenue, an organisation looks at the sales department, whereas for maximising profits, it looks at materials management. Lean Supply Chain Management is a philosophy that champions waste reduction and process simplification. It’s a systematic approach to streamline both material and information flow, ensuring responsive and cost-effective supply chain networks. This approach necessitates close collaboration between vendors, manufacturers, distributors, and customers. By working together closely rather than operating as separate entities, organisations can streamline processes, minimise waste, and improve overall delivery of value to customers.
INPUT (MONEY) X |
OUTPUT(MONEY)X + Y Max |
TRANSFORMATION PROCESS (PLANT + MACHINES + EMPLOYEES + MATERIALS + METHODS). TIME BEING COMMON RESOURCE.PROCESS (PLANT+MACHINES+EMPLOYEES + MATERIALS + METHODS)RMATIONPROCESS (PLANT+MACHINES+EMPLOYEES + MATERIALS + METHODS) |
The Lean and Six Sigma methodologies combined together are effective exclusively for optimising supply chains. This approach brings together specifically a unified focus on two essential aspects of manufacturing: efficiency and quality.
The 5 principles of lean management
- Identify Value: Understand & determine what the customer values and focus on creating that value.
- Value Stream Mapping: Verify, analyse, and map out all steps in the process to identify and eliminate waste.
- Develop continuous workflows: Ensure that SOP is in place & production processes flow smoothly and without interruptions.
- Create a Pull System: Produce only what & when it is needed to reduce excess inventory and overproduction.
- Seek Perfection with Continuous Improvement: Strive for on-going enhancements in all processes to eliminate waste and increase value.
These lean management principles are universally accepted tools to reinforce & strengthen overall company performance. They are relevant in various businesses and production processes, such as lean manufacturing and lean software development, where the intent is on reducing waste, streamlining operations, and improving quality. Combining Lean with Six Sigma further enhances this approach by not only eliminating waste but also reducing variability and defects, resulting in a more efficient and higher-quality supply chain. On average, product costing typically breaks down as follows:
- Materials: 60%–70% of the product cost.
- Labour: 20%–30% of the product cost.
- Profit: 10%–20% of the product cost.
Indeed, automobile manufacturers are one of the examples that have implemented a “just-in-time inventory system” to reduce waste and improve efficiency. Another example of effective supply chain management is a business that has automated its procurement process to reduce costs & improve vendor communication. The Toyota Motor Company is renowned for its implementation of the Just-In-Time (JIT) inventory system, lean manufacturing, & continuous improvement, which significantly reduces waste and enhances efficiency by producing only what & when it is needed. This approach minimises excess inventory and associated costs, allowing for a more streamlined and responsive supply chain.
By leveraging automation, the company can reduce costs, streamline operations, and improve communication with vendors, leading to more efficient procurement and better vendor-supplier relationships.
5% REDUCTION IN MATERIALS COST RESULTS IN 30% INCREASE IN RETURN ON INVESTMENT (ROI).
SALES Rs. 5000/- |
LABOUR Rs. 700/- |
RS IN LAKHS
PROFIT Rs. 400/- |
(MINUS)
PROFIT MARGIN 8% |
PRODUCTION COST Rs. 3800/- |
MATERIALS Rs. 2300/- |
SALES Rs. 5000/- |
MARKETING EXPENSES Rs. 800/- |
OVERHEAD Rs. 800/- |
DIVIDED BY
( (10.3%)
RETURN ON INVESTMENT (ROI) 10.0% |
MULTIPLY
INVENTORY Rs. 500/- |
SALES Rs. 5000/- |
CURRENT ASSETS Rs. 1100/- |
(13.0%)
ASSET TURNOVER RATE 1.25 |
BILLS RECEIVABLES Rs. 300/- |
DIVIDED BY
TOTAL ASSETS Rs. 4000/- |
PLUS (1.26)
FIXED ASSETS Rs. 2900/- |
CASH Rs. 300/- |
LEAN SCM – ILLUSTRATION:
TRANSFORMATION PROCESS ( MATERIALS ). PROCESS (PLANT+MACHINES+EMPLOYEES + MATERIALS + METHODS)RMATIONPROCESS (PLANT+MACHINES+EMPLOYEES + MATERIALS + METHODS) |
INPUT (MONEY) X |
OUTPUT(MONEY)X + Y Max |
· HOW FAST
· HOW EFFICIENT
A petty street vendor borrows rupees 10,000/- (ten thousand only) from a money lender at an extreme 24% interest rate as no bank was willing to lend him money. Also, due to severe competition in the market, the vendor cannot think of a profit more than 10% (ten percent) margin. Even with such a restriction, the street smart vendor could make a comfortable profit. HOW IS IT?
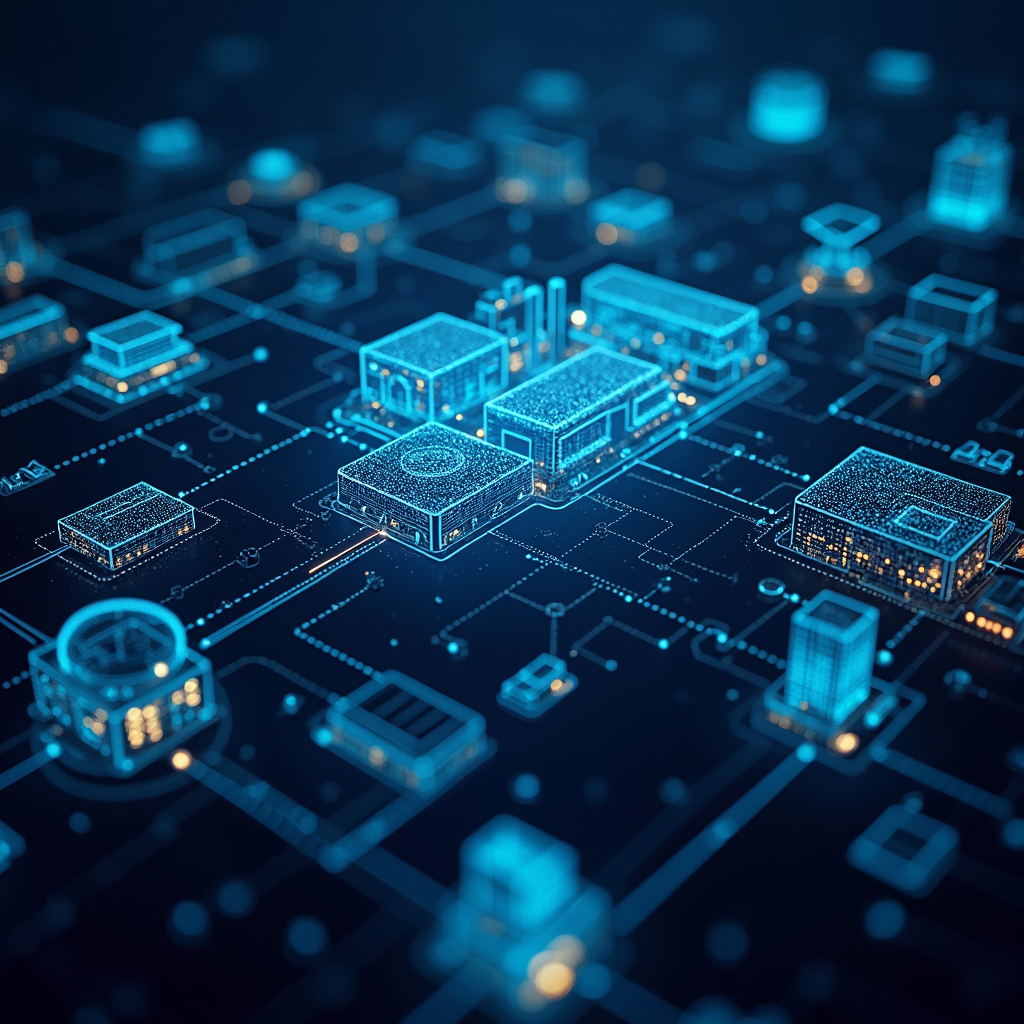
If the inventory turnover ratio is one year, the street vendor earns Rs. 11,000/- only, whereas he has to repay Rs. 12,400/- including interest, there being a loss of Rs. 1400/- during the year. Earns Rs. 11000/- during the year, there being a LOSS of Rs. 1400/- against the loan to repay. However, if the inventory turnover ratio (cycle time) is at an interval of (2) months, the street vendor earns Rs. 11,000/- repayment being Rs. 10,400/- including interest, there being a profit of Rs. 600/- in one cycle of two months, thus against (6) cycles the profits would be Rs. 600 x 6 (cycles) = Rs. 3600/- annually. If the inventory turnover ratio (cycle times) is at an interval of (2) months, the PROFIT is Rs. 600/-.
Disadvantages of Poor Supply Chain Management
Factors like responding to uncertain weather conditions, poor inventory management, the inability to predict demand, and poor 3PL/5PL management & compliance trigger a series of uncertainties and inefficiencies across a supply chain. This creates a domino effect, adversely impacting the core aspects of a supply chain of businesses.
Every business needs frameworks and systems in place to enable them to progress & succeed each day and thrive for perennial long-term achievement and sustainability. Businesses face crucial challenges in their supply chains where issues like inadequate inventory mismanagement, unreliable suppliers, increasing logistics costs, prolonged production cycles, non-compliances, poor customer experience, and transportation delays can create a ripple effect leading to inefficiency and higher costs. Factors like responding to uncertain weather conditions, inefficient inventory management, inability to forecast demand, & imperfect 3PL/5PL management result in a series of uncertainties, impacting the supply chain network of businesses. However, following are the ways for companies to address challenges; by adopting these strategies, businesses can mitigate risks of supply chain disruptions, resulting in efficient operations and long-term success:
- Effective Inventory Management:
- Automated procurement process & restocking: Use real-time data to automatically manage stock levels, reducing the risk of running out or overstocking items.
- Inventory Control Techniques: Implementing systems like Just-in-Time (JIT) to keep inventory at the right levels, ABC, FSN, XYZ analysis, minimising holding costs, and ensuring availability.
- Reinforce Supplier Relationship Management (SRM):
- Supplier Diversification: Work with multiple suppliers to reduce the risk of disruption if one fails to deliver.
- Collaboration with Suppliers: Build strong, perennial communicative relationships with suppliers, using tools to monitor performance and align objectives.
- Better Demand Forecasting:
- Data-Driven Analytics: Use big data and machine learning to forecast customer demand more accurately, helping businesses stay ahead of market fluctuations.
- Collaborative Planning: Work closely with supply chain network partners to share insights and create more accurate forecasts.
- Streamlined Transportation:
- Transportation Management Systems (TMS): Use software to lower costs, optimise delivery routes, and track performance in real-time.
- Effective Management of Logistics Partners: choose and manage logistics providers prudently to ensure they meet service expectations.
- Risk Management and Compliance:
- Risk Assessment: Assess potential risks periodically, like weather disruptions or supplier issues, and always have contingency plans.
- Compliance Monitoring: Be familiar with and up to date with regulations to ensure that supply chain meets necessary standards and avoids penalties.
- Enhanced Communication and Collaboration:
- Integrated Platforms: Use tools that enable real-time communication across the supply chain, from suppliers to intermediaries and customers.
- Regular Meetings: Foster regular communication among all parties involved to quickly address and resolve issues.
The efficiency levels of a supply chain have the power to make or break businesses. Businesses manage their supply chain by two of the most important competitive differentiators: price and customer experience.
An inefficiently managed supply chain can lead to significant costs for a business and can adversely impact a company, as stated below:
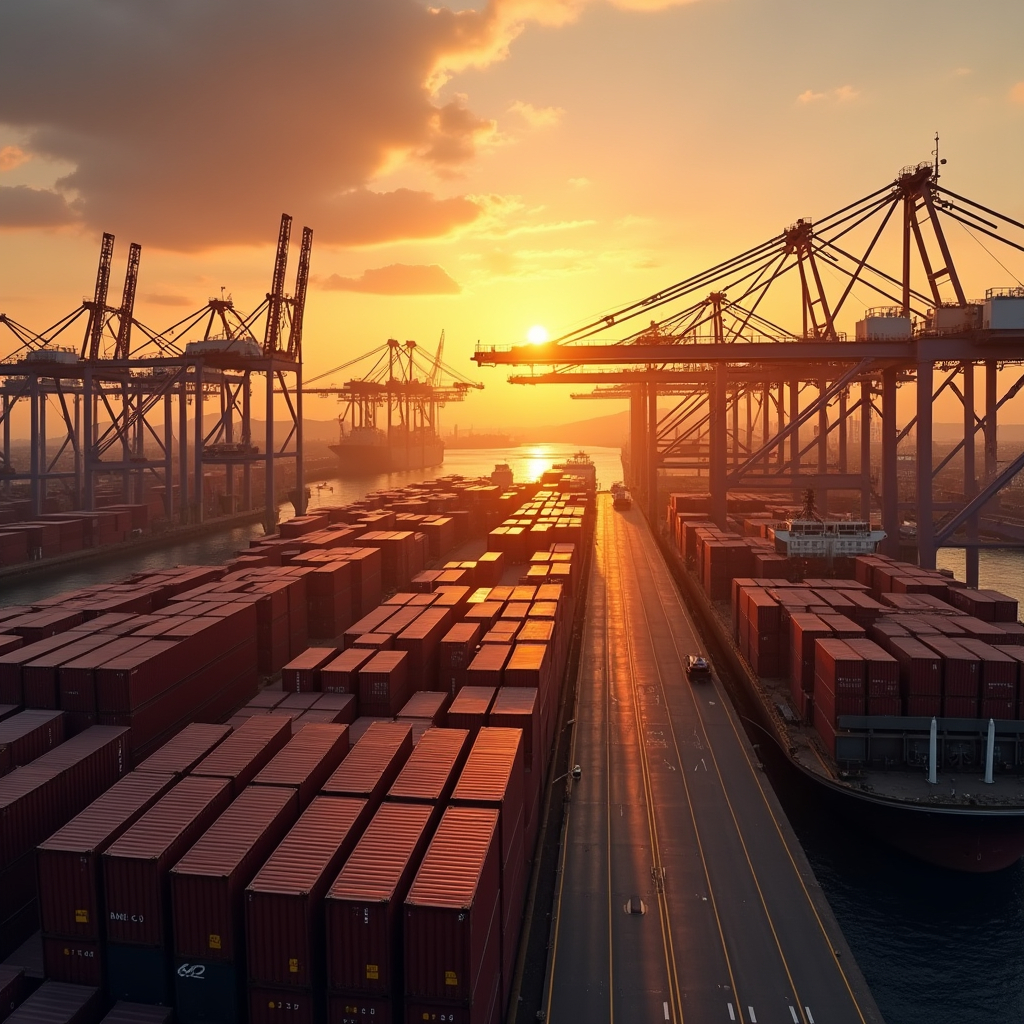
- Mismanaged Implementation:
- To upgrade & change supply chain management, systems require financial resources, valuable time, and the energy of human resources. If not implemented properly, there will be wasted labour, service redundancy, and missed deadlines, which can be costly.
- To prevent these issues, top logistics providers conduct thorough analysis before making changes. They ensure to fully survey, understand & identify consolidation opportunities, assess the client’s shipping schedule, and evaluate last-mile delivery needs to ensure the new system is effective and efficient.
- Inadequate Training:
- Integrating a new system into an existing supply chain often requires restructuring and training team members & is a complex process. Without careful planning and flawless, transparent communication, the process can lead to costly errors and increased employee turnover.
- When selecting logistics providers, it’s essential to ask about their ease of use of their technology and training process. A skilled provider should offer a well-defined onboarding training or transition process that can be customised to fit unique teams and timelines.
- Attitude & Mentality:
- Shortsighted logistics providers who are only focused on getting the contract miss out on opportunities to optimise the supply chain for their clients. While initial savings might be realised, there is every possibility to lose potential long-term savings and growth opportunities.
- Industry-leading logistics providers focus on persistent ways to reduce costs and enhance efficiency for their clients. In order to avoid falling behind their peers, a forward-thinking approach helps businesses sustain one’s supply chain, and businesses can stay ahead in a competitive market and scale higher levels of success than ever before.
A company that excels in supply chain management understands how to address these challenges to avoid the adverse consequences that may arise. Effective supply chain management not only reduces costs but also ensures that resources are utilised efficiently and effectively to their optimum level. By focusing on strong management, cost reduction, and risk mitigation, a business can maintain a competitive edge and achieve greater success.
For companies with complex supply chains, partnering with a supply chain management provider can be particularly advantageous. Such providers help streamline daily seamless operations and take stress off their administrative support teams. While some disruptions are not under our control, most of them can be managed using modern integrated technologies.
Challenges and limitations
Today, SCM challenges faced by companies are as follows:
- Ignoring continued growth of e-commerce, a channel for the industrial sector: As e-commerce continues to expand, especially in the industrial sector, companies that fail to adapt may miss significant opportunities. Ignoring this channel can hinder growth and competitiveness.
- Least attention to potential risks: The volatile transportation costs and commitment to delivery lead times pose substantial risks. Companies that do not manage these risks would face increased costs and compromised service levels.
- Dependency on past performance to forecast sales in the future: Using past performance to forecast sales can be unreliable, especially in dynamic markets. This approach may lead to inaccurate forecasts, resulting in either excess inventory or stockouts.
- Lack of in-depth understanding of the full capacity of suppliers & service providers: A lack of insight into the full capabilities of suppliers, vendors, and service providers can lead to inefficiencies and missed opportunities for optimal supply chain network utilisation.
- Waiting for SCM technology to fix everything holistically by minimising the complexity of supply chain activities & eliminating the introduction of unnecessary technology: While technology can streamline supply chain activities, relying on it to solve all issues without considering the complexity of operations can lead to oversimplification and missed opportunities for improvement.
Though tightly controlled inventory and just-in-time (JIT) manufacturing can reduce costs, they can also leave a company vulnerable if any part of the supply chain fails. The downsides include potential delays, stockouts, and an inability to respond to sudden demand spikes. However, in stable environments with predictable demand, a lean supply chain can be highly effective. In terms of internationalisation and market expansion, supply chain management faces additional challenges. One major issue is the governance gap, where insufficient regulation of corporate activities abroad can lead to human rights violations in supply chains, with companies not held accountable.
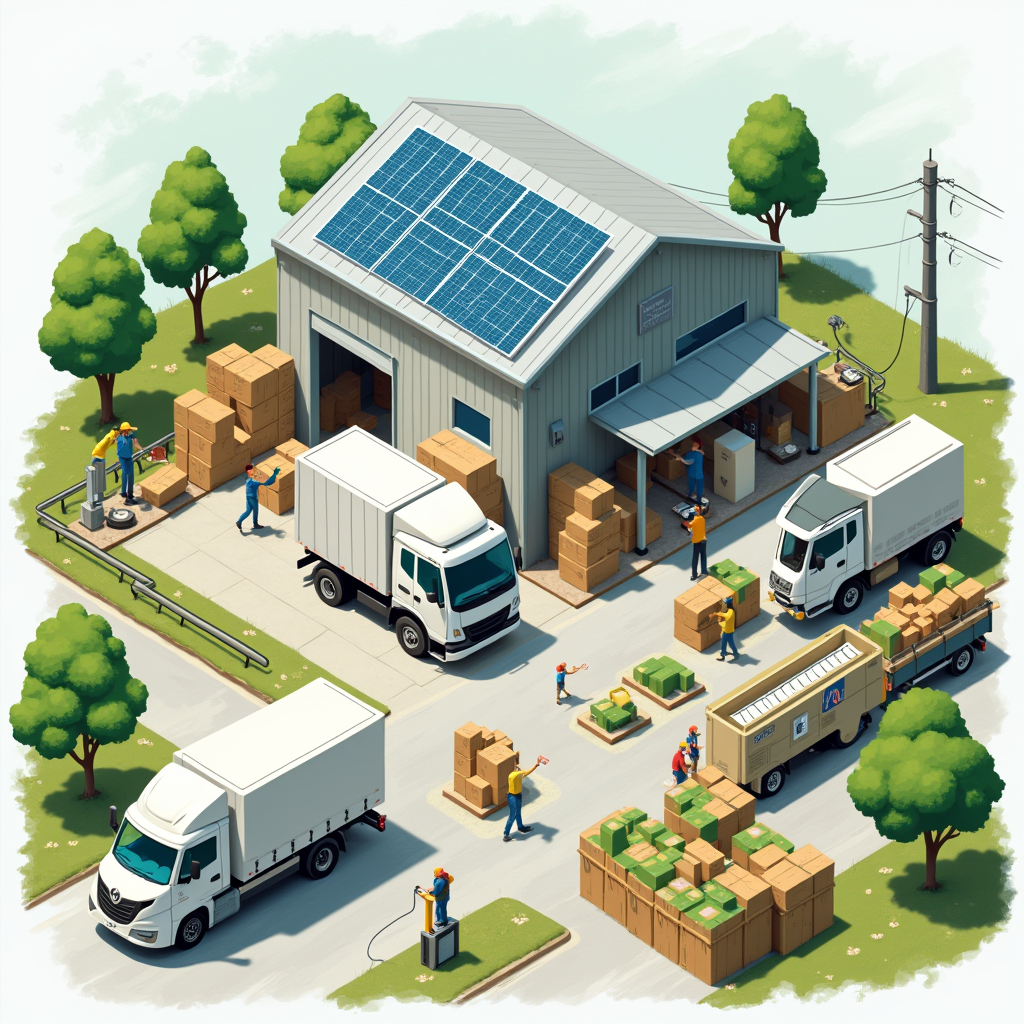
Supply chain management is inherently complex, involving numerous stakeholders like suppliers, carriers, producers, information systems managers, logistics managers, and customers. A supply chain manager’s role is to coordinate the routing of goods, manage inventory, and optimise overall operations, ensuring that the supply chain runs smoothly and efficiently.
Benefits of lean supply management
The benefits of lean supply chain management are significant, which include
- Reduced Costs: By eliminating waste and optimising processes, companies can significantly reduce overall operational costs.
- Improved Communication and Coordination: Lean practices enhance collaboration across the supply chain, leading to better transparent, seamless communication and coordination among all stakeholders.
- Increased Efficiency: Streamlining processes and reducing unnecessary steps & activities results in more efficient operations.
- Improved Customer Satisfaction: Faster, more trusted, reliable deliveries and better-quality products lead to higher customer satisfaction.
- Environmental Benefits: Lean practices often lead to reduced energy consumption in an environmentally friendly atmosphere.
Conclusion
Lean Supply Chain Management (SCM) plays a crucial role in helping organisations achieve higher profitability by enabling faster, more efficient turnover of investments and the most efficient transformation process. While lean principles focus on reducing waste and optimising processes, leading to quicker turnover times and more efficient operations. One of the greatest examples is Toyota Motor Company’s approach to lean supply chain management; it is so effective that they measure turnover in hours rather than months or years, setting them apart from many other organisations. The concept of lean manufacturing and continuous improvement is ingrained deeply in its company culture. The supply chain management in terms of internalisation and market expansion faces several limitations. One of the major limitations is the lack of governance and regulation of corporate activity abroad, which leads to a governance gap.
LEAN, As everybody’s interest is to maintain their body slim and trim without flab, so also every organisation is realising that if they have to be competitive in the market, they have to be lean without flab. Here the word “flab” stands for all kinds of wastes existing in the organisation.
Organisations strive to be lean by eliminating waste (referred to as “Muda,” a Japanese term in lean terminology). Muda represents any activity that consumes time and resources but does not add value to the customer, whether internal or external. It is important to understand that lean is not a quick fix for a management problem but a philosophy, just like yoga, continuously to be practiced in an organisation in conquering the waste (muda). By consistently applying lean principles, organisations can effectively minimise waste and enhance their overall performance.
References
- WWW.Study.com
- Indian Institute of materials management, Navi Mumbai, Bi-monthly magazines (2018 & 2023).
- NLPA (Next level purchasing association) USA, Articles- on SCM-Feb’2018 & May’2022.
- WWW.google.com
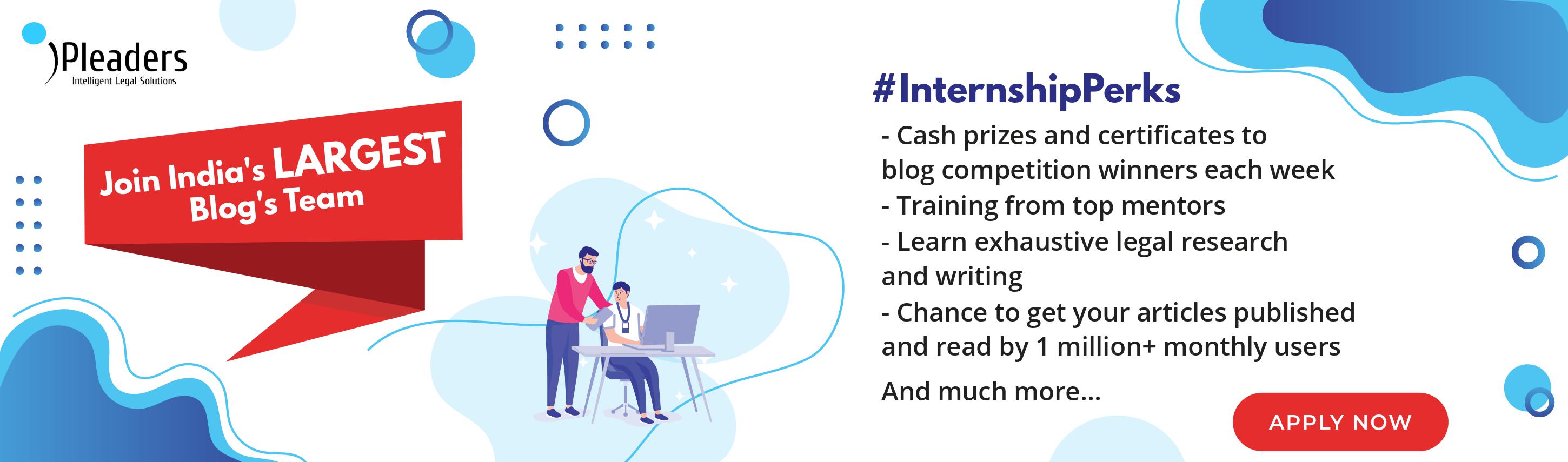